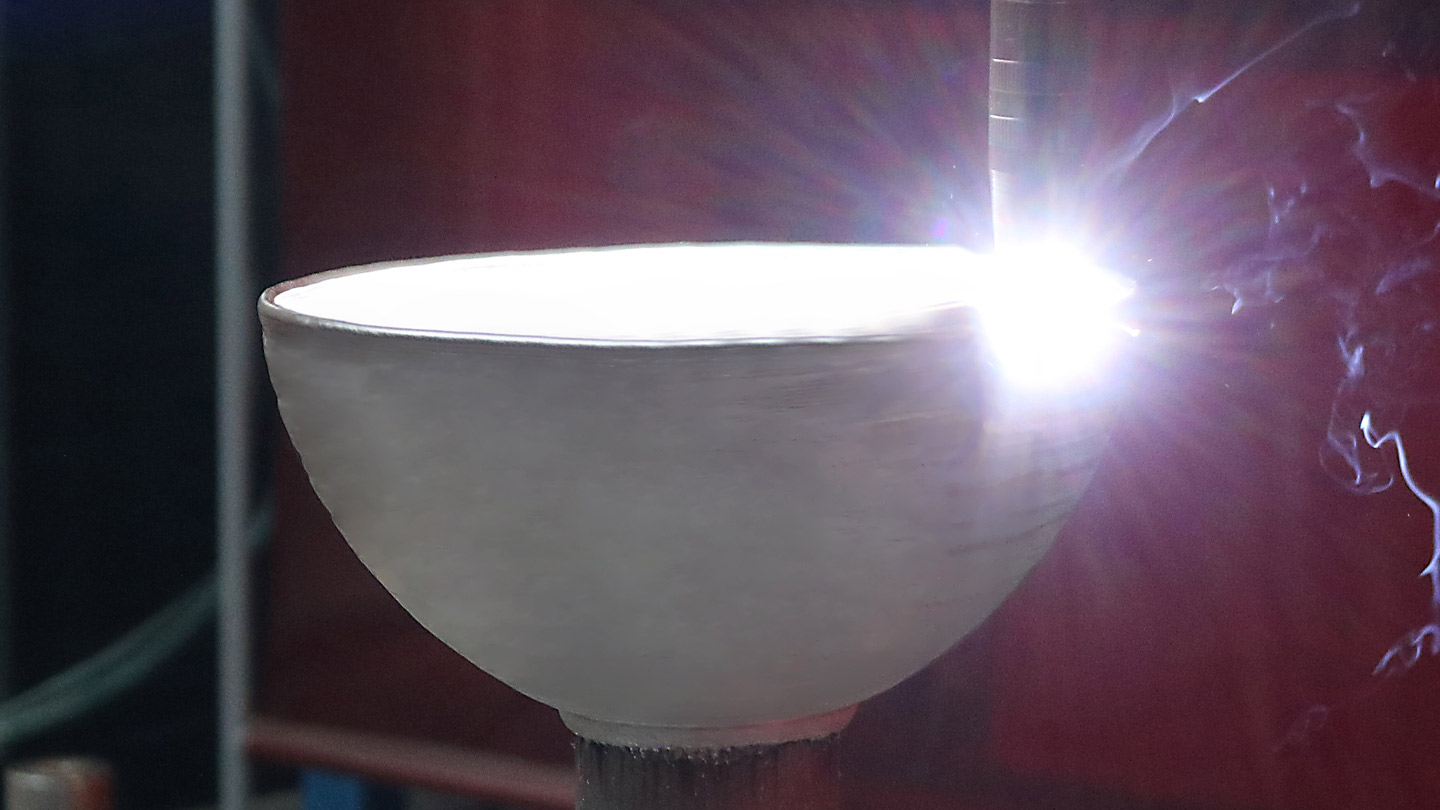
The global aerospace industry is experiencing a great push for innovation, thanks to the huge public and private investments that are fuelling the growing space race and the expansion of the industry.
The European Union identified the space sector as a strategic driver for manufacturing growth in EU countries, and Italy has earmarked several billion euros in investments to this end. Alongside private investments and the work of public agencies like ESA, new business models for space services are emerging. As a result, the demand for advanced components for specific space applications is growing and the importance of directing as much investment into the development of innovative manufacturing technologies is becoming apparent. The aim is that of producing an ever-increasing number of space vehicles and applications on time, sustainably, and efficiently.
Additive Manufacturing is playing a key role in this evolution, thanks to its characteristics of flexibility, sustainability, and cost-effectiveness on small production volumes. The aerospace sector, which has always been characterized by low production volumes, long lead times, and advanced components made with traditional manufacturing techniques, immediately grasped the enormous potential and benefits that can be derived with new technologies.
Following on this trend and all the work Caracol has been conducting in the aerospace sector, thanks to the TechFast Lombardia call (POR FESR 2014-2020), the company has been working on a project to manufacture space applications in a more efficient way, such as pressure tanks. The overall aim is to support the technological and digital innovation of production processes through additive, to expedite small and medium-sized space enterprises’ work.
The final part chosen for this tender is a pressurized tank, manufactured with a lightweight aluminum alloy AL2319, which will be mounted on a carrier satellite to transport and release CubeSats into orbit. Once in orbit, these satellites are used for research, telecommunications, and monitoring operations in both research and commercial applications. Caracol has developed advanced manufacturing solutions for the on-demand production of custom metal components for the aerospace sector. Specifically, the WAAM technology developed is based on a MIG (Metal Inert Gas) welding technology and can be used to produce finished parts for advanced sectors. Furthermore, leveraging its extensive know-how in programming and designing advanced additive manufacturing robotic systems, as well as the experience in hardware-software integration gained with the large-scale Fused Granular Fabrication (FGF) process, Caracol developed and deployed its proprietary slicing and control software for WAAM, that works on 8-axis.
To conduct this project, Caracol worked with prominent partners in Lombardy:
– D-Orbit S.p.A., a company operating in the space logistics and transportation services industry. Identified as end-user of the project, they helped pinpoint the functional characteristics the component would need, from the geometry to the test requirements the pressurized tanks would need to meet.
– The Department of Mechanical Engineering of Politecnico di Milano, was fundamental for material characterization, the testing phase for the qualification of the final product, and in the definition of the process parameters optimization.
In addition to the hardware and software innovations that derived from this project, Caracol and its partners also designed and assessed a Digital Flow to integrate engineering, manufacturing, and testing processes to produce metal aerospace components. The elements of digital innovation introduced in the project refer to three main fields: software, control, and automation. The integration of these three aspects leads to a highly automated and efficient workflow. Furthermore, the identification of a Digital Flow to control each process phase allows WAAM technologies to guarantee repeatability and control over the process, ensuring these processes can become an effective and efficient alternative to traditional manufacturing technologies.
01 Pressurized Tanks for Space with WAAM
02 Pressurized Tanks for Space with WAAM
THE BENEFITS OF CARACOL’S WAAM SOLUTION FOR ADVANCED AEROSPACE APPLICATIONS
Traditional manufacturing techniques face several critical issues in terms of efficiency and sustainability, part weight, design adaptability, and customizability. Filament winding is the most renowned technology, also used by NASA for pressurized tank applications since the ‘80s. Although it guarantees high speed and precision in manufacturing, it bears very high costs for complex geometries and low volumes, combined with operational complexities in the process, it can create only standard shapes that are limited to axisymmetric geometries and requires a lot of manual operations.
Caracol decided to pursue WAAM as a solution for these applications as it brings numerous advantages in terms of design flexibility, performance, efficiency, and foster sustainability. With regards to the product, it combines the significant reduction of scrap material with an optimized design, allowing for weight reduction of the final component. Applied to the specific case of the pressurized tank installed in a satellite carrier, this leads to considerable cost savings, on both production and launch and a positive environmental impact – as the amount of propellant required for the launch depends directly on the spacecraft’s mass. On the other hand, in terms of process, WAAM technology allows to produce a mono-material propellant tank. For high-demand applications, this technology can potentially be used in combination with filament winding, to effectively provide metal cores with complex shapes.
The main advantages seen in the project were:
- possibility of producing complex, be-spoke geometries, without any shape constraints;
- greater freedom in the design of parts;
- possibility of obtaining a high-performance metal structure with a monolithic component, without having to assemble several parts (shells, cores, mandrels, fittings);
- possibility of managing the process through digital workflow;
- reduction of lead time;
- reduction of waste and raw material used vs. traditional tech (e.g., subtractive processes)
In conclusion, this project assumes great relevance as it shows the tangible potential of an early-stage technology like WAAM for the production of space-finished parts. Today, WAAM has still a long way to go to extend its employment, not only in Lombardy but also in Italy and Europe. The technology brings with it all the product and process benefits of additive manufacturing and Caracol’s know-how on AM with robotic systems, expanding its potential to the application of propellant tanks for space crafts. Today, Caracol keeps working on the project with a feasibility study to make this metal 3D printing technology and its WAAM solutions ready for use across advanced industrial industries.