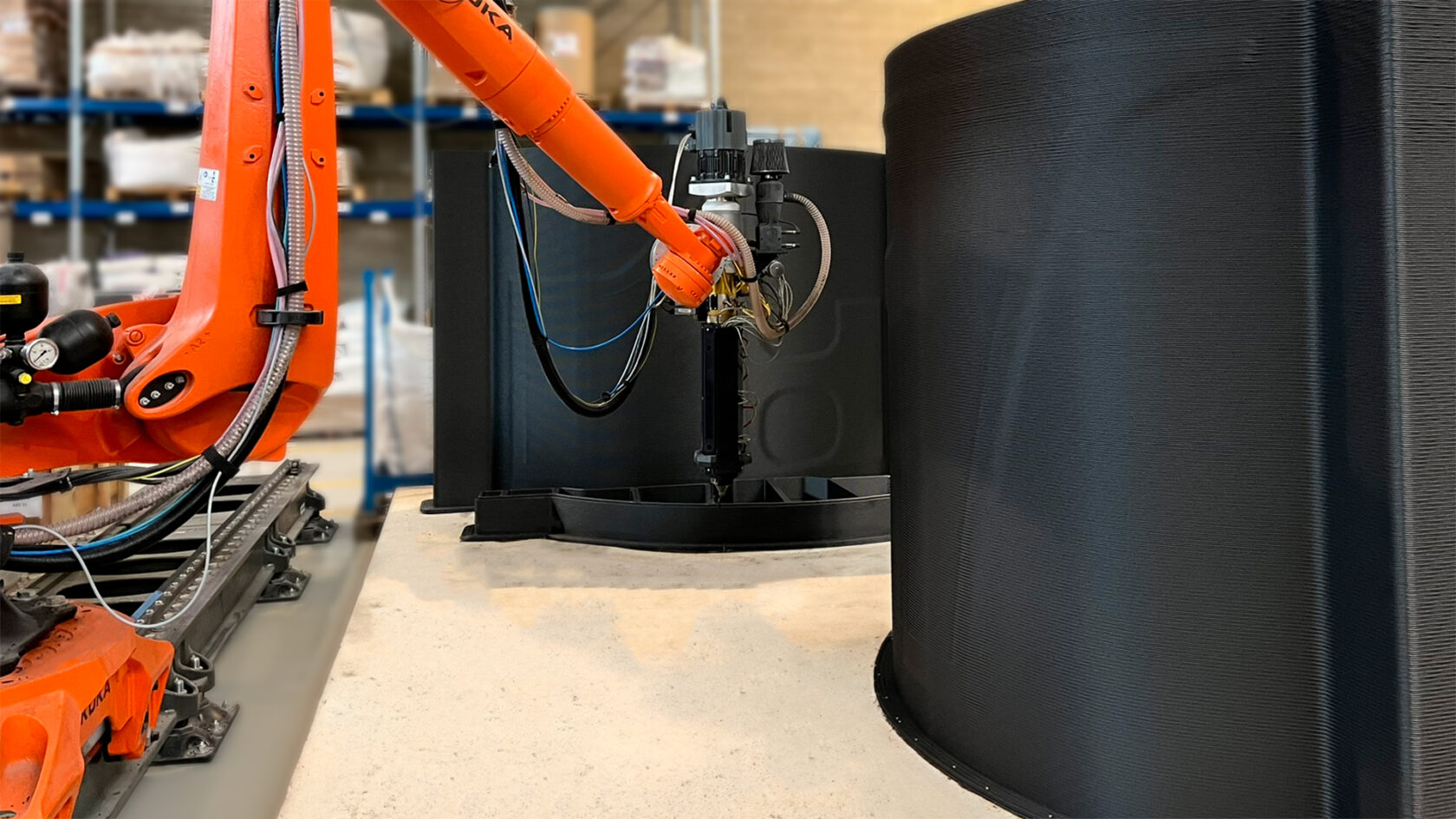
La stampa 3D di grande formato, come quella sviluppata da Caracol, sta rivoluzionando i processi produttivi nei settori più esigenti, tra cui l’aerospaziale, l’energetico e l’automobilistico. Grazie alla sua flessibilità progettuale, la rapidità di produzione e la migliore efficienza, le tecnologie LFAM sono capaci di superare i limiti dei metodi di produzione tradizionali, aprendo nuove frontiere per l’innovazione industriale.
La tecnologia robotica LFAM chiavi in mano di Caracol – Heron AM – consente la produzione di mega tool dalle geometrie complesse con materiali compositi, ottenendo diversi vantaggi di processo, dai costi alla sostenibilità al peso, rispetto ai metodi tradizionali. La capacità di Heron di stampare praticamente senza limiti di dimensioni, sfruttando i movimenti a 6+ assi del robot, offre una maggiore flessibilità nella produzione di tool, eliminando la necessità di assemblaggi, riducendo significativamente il materiale utilizzato ed i relativi scarti, accelerando in ultimo i tempi di produzione.
Caracol ha dimostrato con successo questi vantaggi attraverso varie applicazioni, producendo tool robusti customizzati per soddisfare le specifiche esigenze industriali.
1. Tool per dime di rifilatura e foratura
I metodi di produzione tradizionali, pur garantendo la precisione necessaria per soddisfare i rigorosi standard dell’industria aerospaziale, presentano significative inefficienze e un elevato impatto ambientale. Questi processi richiedono l’uso di diverse leghe metalliche, come Invar e Alluminio, per realizzare un singolo componente, oltre a fasi complesse di saldatura e assemblaggio, e a una gestione complicata delle forniture di materie prime. Di conseguenza, l’industria aerospaziale affronta costi elevati, processi altamente laboriosi e tempi di consegna prolungati.
Queste criticità si amplificano nella produzione di tool specializzati, come dime per rifilatura e foratura, fondamentali per assemblaggio e manutenzione. La realizzazione di questi strumenti richiede cicli produttivi lunghi e un lavoro manuale estremamente accurato, rallentando ulteriormente i processi.
La tecnologia LFAM rappresenta un’alternativa innovativa, consentendo di produrre tool compositi e leggeri in un unico processo, riducendo drasticamente le necessità di assemblaggio e i tempi di consegna. La stampa 3D offre inoltre maggiore flessibilità progettuale, tempi di produzione più rapidi e l’impiego di materiali termoplastici avanzati e riciclabili, ottimizzati per le specifiche esigenze dell’industria aerospaziale.
Di seguito sono riportati due esempi di tool stampati in 3D che mostrano come l’adozione di Heron AM nella produzione di maschere di rifilatura e foratura possa aumentare l’efficienza nell’industria aerospaziale.
Maschera di posizionamento – dati rilevanti:
- SISTEMA: Heron 400
- ESTRUSORE: High Flow (HF)
- DIMENSIONE UGELLO: 12 mm
- MATERIALE: ABS + 30% Glass Fiber
- POST-PPRODUZIONE: Machining
- DIMENSIONE: 1800 x 1600 x 700 mm (singolo pezzo)
- PESO: 400 Kg (singolo pezzo)
- TEMPO DI STAMPA: 16 hrs (singolo pezzo)
- RIDUZIONE DEL PESO: 70%
- RIDUZIONE DEL TEMPO DI PRODUZIONE: 80%
- RIDUZIONE DEI COSTI: 30%
Tool per la rifilatura e foratura – dati rilevanti:
- SISTEMA: Heron 400
- ESTRUSORE: High Flow (HF)
- DIMENSIONE UGELLO: 12 mm
- MATERIALE: ABS + 20% Carbon Fiber
- POST-PRODUZIONE: Machining
- DIMENSIONE: 1700 x 1500 x 2200 mm
- PESO: 600 Kg
- TEMPO DI STAMPA: 30 hrs
- RIDUZIONE DEL PESO: 70%
- RIDUZIONE DEL TEMPO DI PRODUZIONE: 80%
- RIDUZIONE DEI COSTI: 30%
2. Tool per la polimerizzazione in autoclave
Il settore automobilistico affronta diverse sfide nella produzione di tool per la polimerizzazione in autoclave, indispensabili per la lavorazione di parti in composito come quelle in fibra di carbonio. I metodi tradizionali prevedono spesso l’incollaggio di più lastre in resina o metallo per raggiungere il volume richiesto, seguito dalla fresatura della superficie. Questo processo comporta un’elevata complessità produttiva, un maggiore consumo di materiale, un aumento della manodopera e, di conseguenza, tempi di consegna più lunghi.
Caracol propone una soluzione innovativa grazie alla stampa 3D, offrendo Direct Mold leggeri, dalle geometrie complesse, realizzati in un unico pezzo con materiali termoplastici avanzati. La tecnologia Heron AM consente una progettazione altamente flessibile, ottimizzando le forme già nella fase di ingegnerizzazione, riducendo al minimo il materiale utilizzato e accelerando significativamente i tempi di produzione. Questo approccio rende il processo più efficiente, sostenibile e adattabile alle esigenze del settore.
Gli strumenti stampati in 3D per autoclave, inoltre, possono essere realizzati con materiali avanzati, in grado di garantire una maggiore durabilità e resistenza alle condizioni estreme dei cicli di autoclave, migliorando così l’efficienza complessiva della produzione automobilistica.
A seguire, un caso di studio di successo di Caracol che evidenzia i vantaggi della stampa 3D nella creazione di un Direct Mold ideale per la produzione in serie ridotta di componenti automobilistici.
Dati rilevanti:
- SISTEMA: LFAM Heron 400 with HF extruder
- DIMENSIONE UGELLO: 12mm
- MATERIALE: PC + 20% Carbon Fiber
- POST-PRODUZIONE: Machining + Autoclave
- DIMENSIONE: 1700 x 2000 x 1000 mm
- PESO: 700 Kg
- TEMPO DI STAMPA: 37 hrs
- RIDUZIONE DEL PESO: 70%
- RIDUZIONE DEGLI SPRECHI: 60%
- RIDUZIONE DEL TEMPO DI PRODUZIONE: 70%
- RIDUZIONE DEI COSTI: 20%
3. Tool per la laminazione di micro-pale eoliche
Il tooling è essenziale per la produzione di pale leggere e ad alte prestazioni, che spesso richiedono design precisi e geometrie complesse per ottimizzare l’efficienza aerodinamica. I metodi di produzione tradizionali, come la lavorazione e la fusione, faticano a soddisfare queste esigenze e a rimanere efficienti a causa dei lunghi tempi di consegna, dell’elevato spreco di materiale e della limitata flessibilità di progettazione.
La stampa 3D di tool per la produzione RTM di parti di laminazione è una soluzione all’avanguardia, che consente la produzione di tool di laminazione personalizzati in un unico pezzo. LFAM riduce gli sprechi di materiale, abbrevia i cicli di produzione e consente l’uso di materiali avanzati riciclabili, studiati per resistere alle difficili condizioni ambientali delle turbine eoliche.
La sezione seguente mostra un progetto di successo realizzato da Caracol (in collaborazione con Deremco, Acus e Carbon Cleanup), in cui l’adozione di Heron AM ha aumentato la flessibilità di progettazione, ha consentito una prototipazione più rapida e ha migliorato il ciclo di produzione complessivo delle micro-pale eoliche.
Dati rilevanti:
- SISTEMA: LFAM Heron 400 with HF extruder
- DIMENSIONE UGELLO: 12mm
- MATERIALE: ABS + 20% recycled Carbon Fiber
- POST-PRODUZIONE: Machining + Lamination
- DIMENSIONE: 1450 x 450 x 2200 mm
- PESO: 400 Kg
- TEMPO DI STAMPA: 24 hrs
- RIDUZIONE DEL PESO: 85%
- RIDUZIONE DEL TEMPO DI STAMPA: 75%
- RIDUZIONE DEI COSTI: 55%